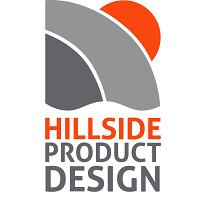
ABOUT
The client is a manufacturer of electrical and electronic test equipment for aerospace, rail and defence vehicles which is experiencing a period of focussed growth and development. They had developed a new system for testing electromechanical connections within assemblies - vital for ensuring that vehicles are safe - but felt that their current test-probes (one held in each hand by the test technician) did not portray the high standards and forward-thinking image they were aspiring to.
Hillside Product Design began an intensive scheme of work to optimise the ergonomic and mechanical aspects of the test probes, with the aim of designing and sourcing high quality injection moulded parts suitable for use in critical environments under stringent control.
In order to simulate the conditions that the probes would be used in – tight spaces within chassis, fuselage and aero engines, a series of tests were devised which required a range of test users to reach to high and low points, position the probes through tight spaces, and apply precise pressures. This was documented by video and collated to form the ergonomic requirements for the product. It was remarkable how many different methods the testers used to reach the same markers, indicating that the devices and their visual outputs must be suitable for use in any variety of orientations without causing discomfort and fatigue.
Once the developed designs for the probes and hand-held controller had been prototyped with Hillside Product Design’s in-house 3D printing facility, the client tested and approved the design for tooling. The tool build was commenced and regular liaison between the toolmaker, the injection moulder and Hillside Product Design was maintained to ensure that the client’s requirements were met.
MADEIT CREDITS
-
Aerospace Test Equipment ManufacturerClient
-
TomSenior Product Designer -
Hillside Product Design